Comprehensive Guide: What is Porosity in Welding and How to Prevent It
The Scientific Research Behind Porosity: A Comprehensive Guide for Welders and Fabricators
Recognizing the intricate devices behind porosity in welding is critical for welders and producers making every effort for impeccable workmanship. From the composition of the base materials to the details of the welding process itself, a multitude of variables conspire to either intensify or ease the visibility of porosity.
Understanding Porosity in Welding
FIRST SENTENCE:
Exam of porosity in welding reveals vital understandings right into the stability and top quality of the weld joint. Porosity, identified by the visibility of dental caries or gaps within the weld steel, is a typical problem in welding processes. These spaces, otherwise appropriately dealt with, can compromise the structural honesty and mechanical properties of the weld, bring about potential failings in the finished item.
To find and quantify porosity, non-destructive testing techniques such as ultrasonic testing or X-ray assessment are usually utilized. These methods enable for the identification of interior problems without endangering the stability of the weld. By analyzing the dimension, form, and circulation of porosity within a weld, welders can make enlightened decisions to boost their welding procedures and achieve sounder weld joints.

Factors Influencing Porosity Development
The incident of porosity in welding is influenced by a myriad of elements, ranging from gas securing performance to the intricacies of welding parameter setups. One vital variable adding to porosity development is poor gas securing. When the protecting gas, commonly argon or CO2, is not efficiently covering the weld pool, climatic gases like oxygen and nitrogen can contaminate the molten metal, resulting in porosity. Additionally, the cleanliness of the base materials plays a considerable role. Contaminants such as corrosion, oil, or wetness can evaporate throughout welding, producing gas pockets within the weld. Welding specifications, including voltage, current, travel speed, and electrode kind, likewise influence porosity development. Making use of incorrect setups can generate too much spatter or heat input, which subsequently can cause porosity. In addition, the welding strategy employed, such as gas metal arc welding (GMAW) or secured metal arc welding (SMAW), can influence porosity development as a result of variations go right here in heat distribution and gas protection. Recognizing and regulating these aspects are necessary for lessening porosity in welding procedures.
Results of Porosity on Weld Quality
The visibility of porosity likewise deteriorates the weld's resistance to corrosion, as the entraped air or gases within the spaces can react with the surrounding setting, leading to deterioration over time. Furthermore, porosity can impede the weld's ability to withstand pressure or effect, more endangering the total quality and dependability of the welded framework. In crucial applications such as aerospace, automotive, or structural building and constructions, where safety and security and sturdiness are vital, the harmful effects of porosity on weld high quality can have severe repercussions, stressing the value of lessening porosity through proper welding strategies and treatments.
Strategies to Reduce Porosity
Additionally, using the suitable welding specifications, such as the right voltage, present, click and travel speed, is essential in avoiding porosity. Keeping a constant arc length and angle throughout welding additionally helps decrease the possibility of porosity.

Making use of the appropriate welding strategy, such as back-stepping or using a weaving movement, can additionally aid disperse warmth uniformly and minimize the opportunities of porosity formation. By applying these strategies, welders can successfully decrease porosity and generate premium bonded joints.
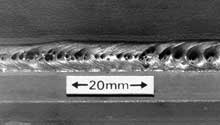
Advanced Solutions for Porosity Control
Carrying out cutting-edge modern technologies and cutting-edge techniques plays a pivotal role in attaining remarkable control over porosity in welding procedures. Furthermore, using sophisticated welding strategies such as pulsed MIG welding or changed atmosphere welding can additionally aid reduce porosity problems.
An additional official website sophisticated option involves using innovative welding devices. As an example, using equipment with integrated functions like waveform control and innovative power sources can improve weld quality and minimize porosity threats. The implementation of automated welding systems with specific control over criteria can dramatically reduce porosity issues.
Moreover, including innovative tracking and assessment technologies such as real-time X-ray imaging or automated ultrasonic screening can assist in discovering porosity early in the welding procedure, permitting immediate restorative activities. Generally, integrating these advanced options can considerably boost porosity control and enhance the total quality of welded components.
Conclusion
Finally, understanding the scientific research behind porosity in welding is important for welders and makers to generate top quality welds. By identifying the elements influencing porosity formation and carrying out strategies to decrease it, welders can improve the total weld high quality. Advanced solutions for porosity control can better improve the welding procedure and make sure a strong and dependable weld. It is necessary for welders to continually enlighten themselves on porosity and apply ideal methods to achieve optimum outcomes.